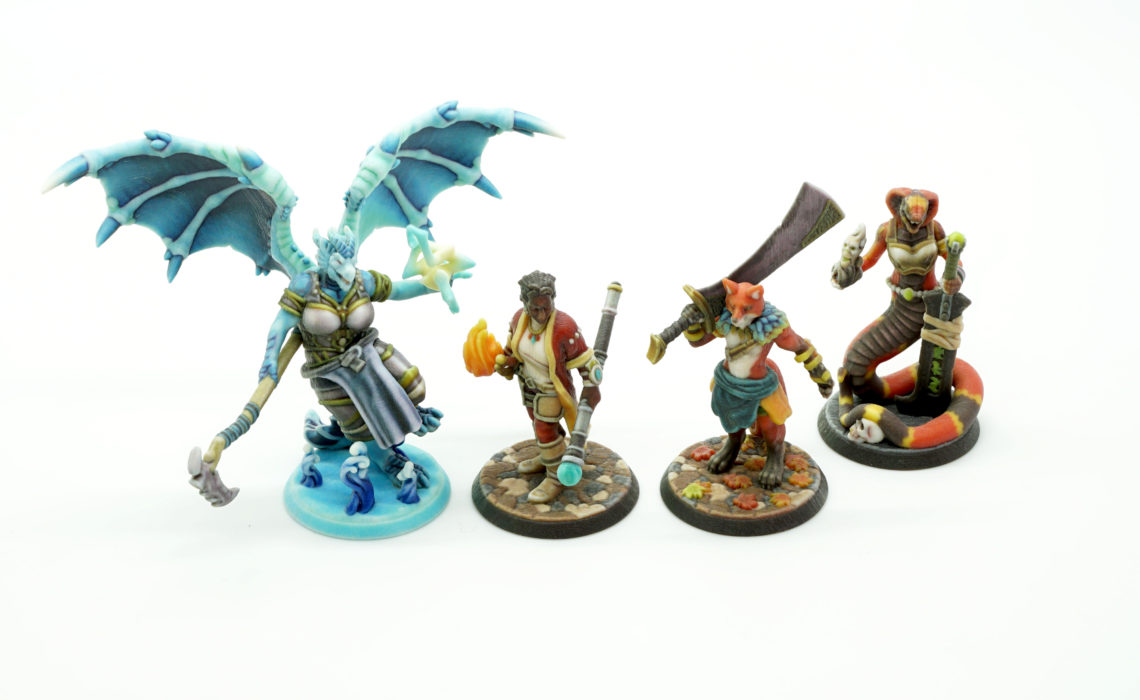
Upon the advent of 3D printing, novelty revolved around the idea of creating a 3D file and converting that into a 3D printed product made layer by layer. Initially intended as a tool for engineers to perform rapid prototyping and improve product development behind the scenes, mainstream companies and organizations soon realized the many benefits involved, beginning with the ability to iterate efficiently.
Bridging the Gaps Between Basic and Full Color 3D Printing
Today, the valued partnership between Shapeways and Mimaki is a highly complementary one with the two companies leading as respective veterans in 3D printing and the application of full color. While industrial manufacturers rely on the technology for rapid prototyping and production of high-performance parts, color 3D printing capabilities have expanded use in applications like gaming too. Tabletop gaming miniatures can be customized with incredible detail for bringing adventure characters to life. There’s no need to settle for parts in basic white or gray anymore though either –especially when you can look forward to 3D printing materials like High Definition Full Color with over ten million hues available.
Used in combination with Material Jetting technology, 3D printed parts are actually white and clear in the middle, with the color applied just around the outside edges.
“If you were to take one of our color prints and cut it in half, what you would see is a mix of white and clear in the center, with color on the outside edge; however, that color on the outside is pigmented resin, so it is the same physical properties as what is building the structure,” says Josh Hope, Sr. Manager, Digital Imaging & Innovation at Mimaki. “We aren’t jetting white and then coloring it—we are actually jetting pigmented resin.”
While even the most basic elements of 3D printing open the door to countless opportunities for innovation, full color 3D printing elevates that process to the next level with great detail for modeling, excellent accuracy and resolution in 3D printing, and unprecedented photorealism in the finished product. Engineers rely on full color for 3D printing in multiple industries, designing for applications like medical modeling for surgical prep, or architecture, presenting intensely detailed models for new developments and accompanying infrastructure.
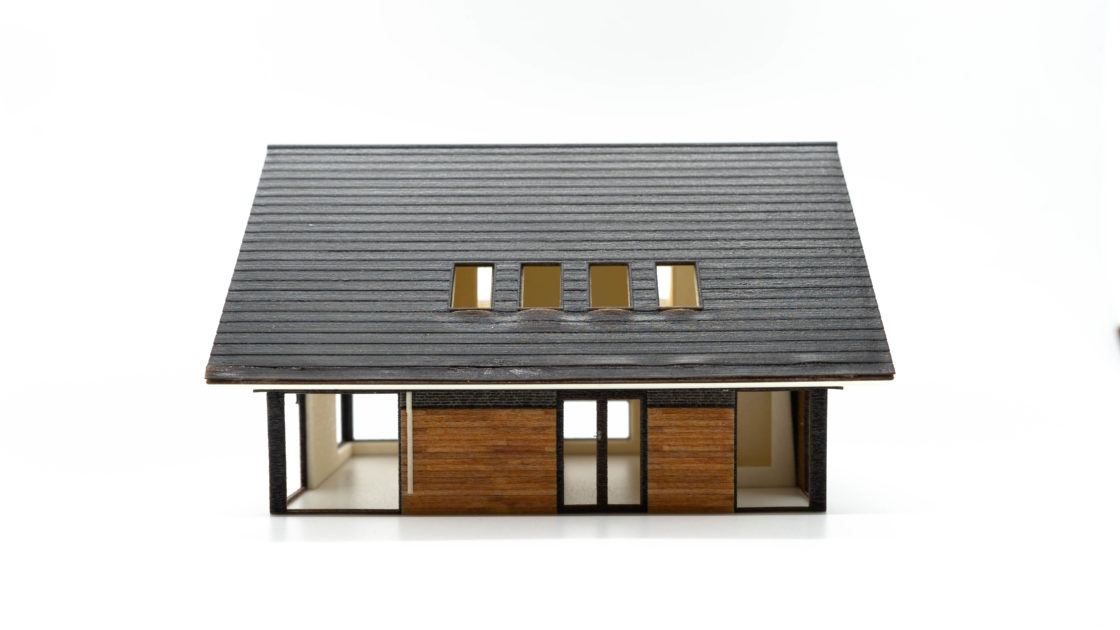
Clean 3D Models Lead to Quality 3D Printed Parts
The first step is to work with a modeling software that offers as many tools as possible on one platform. While Mimaki 3D Applications Specialist Jaime Martinez used free, open-source modeling software like Blender as an example while co-presenting the recent webinar with Shapeways, there are many different products out there, depending on a designer’s preference and project scope. Next, it is imperative for any designer not only to define exactly what it is they are hoping to 3D print, but to also have a full understanding of all the modeling tools with which they are working.
Creating a quality design and 3D model is an integral part of the product development process, relying on an understanding of how to move different mesh designs, along with using the extruding and scaling tools.
“As your experience grows in modifying and adjusting your needs for a model, you will have more control of your mesh,” said Martinez. “No matter what type of project you are designing for, however, a clean mesh is always easier to edit.”
Martinez goes on to stress the importance of honing 3D modeling skills over the idea of trying to re-work downloaded models. While this may be a common temptation, he points out that it is not recommended despite the availability of tools meant for drawing over existing mesh.
“There’s no silver bullet for cleaning up downloaded geometries. Some automated tools can work well, but the best avenue is really just to get better at modeling. While we may enjoy having everything automated, human input is still necessary for specific details in the 3D model and 3D printing parts,” said Martinez. “Humans are still very relevant to this process.”
Continued learning about the process of modeling leads to mastery in creating shapes, or mesh, all a collection of parts which result in viable 3D structures for prototypes or functional, end-use parts. After that, the rest falls into place easily, with basic mesh easily turned into an impressive final structure.
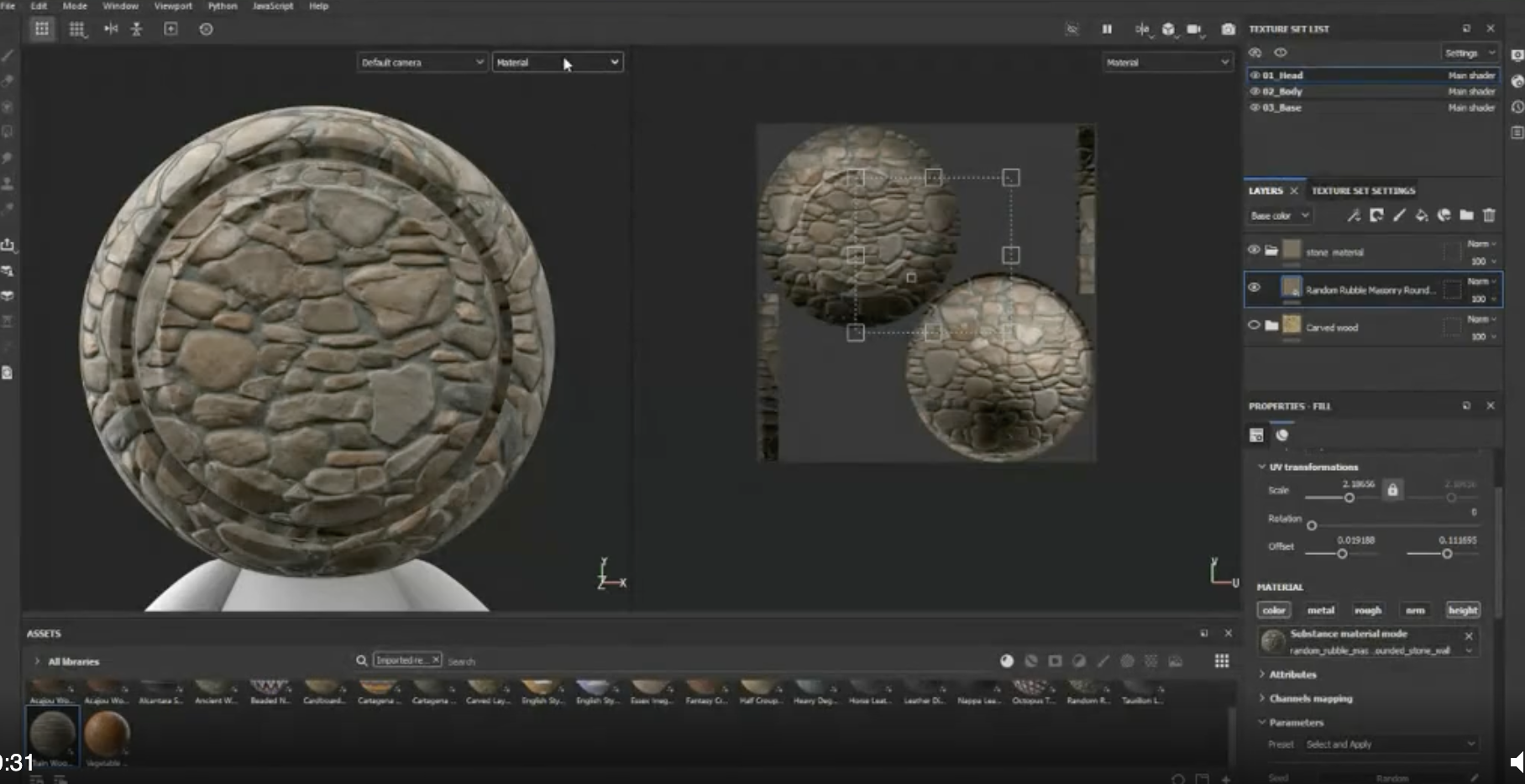
Working with Texture
The use of texturing plays a tremendously important role for many 3D printing projects that include color. While this feature may be used simply to enhance the look of a model, 3D texture can also be applied to hide imperfections like layer lines and ultimately, provide different types of shading.
Texture maps begin with base color, allowing for the option to add a wide array of details that can be manipulated, generally giving products a more authentic look depending on preference and project requirements.
“We usually add details using a black and white image known as a displacement map,” said Martinez. “The black and white image either lifts or lowers the mesh surface. You can use that to your advantage in adding details to your mesh, testing the size of the map and details at first.”
“Effects are applied once you are happy with all the aspects of your mesh.”
Adding full color and texture to a 3D print lead to a combination that’s not only powerful in terms of aesthetics but also for imbuing parts with greater strength. Texture-based workflows are fun for designing smaller pieces like tabletop gaming characters–allowing for amazing details, patterns, and enhanced features–but can also be extremely beneficial in industrial settings for high-performance parts made from a wide range of materials. It is also possible to paint color right into a texture during the modeling process.
Design for Supports
For full color 3D printing with Mimaki, supports are required to stabilize parts during printing. Support structures help attach parts to the print bed, decreasing the potential for deformation, and ensuring a better outcome overall.
In designing supports for High Definition Full Color with Material Jetting, every overhang will be projected toward the bottom, requiring a flat surface for the ink, or material, to ‘land’ on. When supports are required, some geometries can inevitably be tricky; however, with proper orientation it is possible to cut down on the excessive use of such structures.
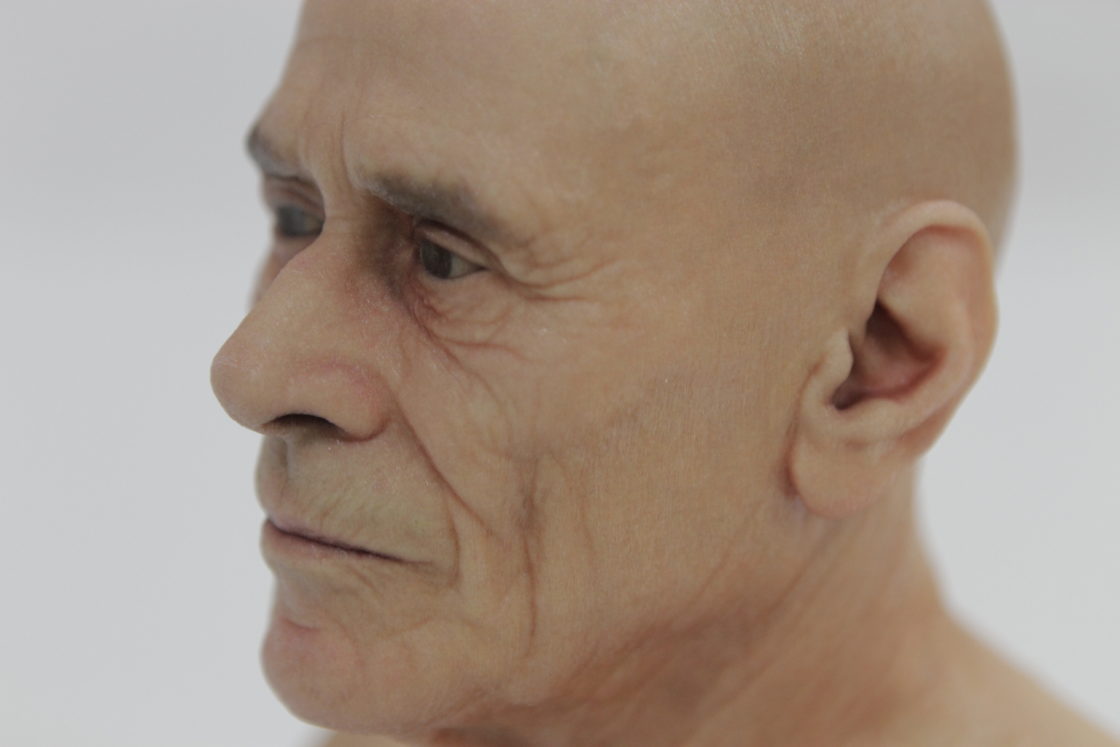
Hollow 3D Printed Products to Minimize Weight and Cost
Hollowing can represent significant savings in material, time, and effort expended in 3D printing, but the designer may also have to determine whether the benefits outweigh the potential for complications in terms of eroding strength of the part, affecting the surface finish, and requiring special requirements for overhangs in some cases.
“If you hollow your part, it may be necessary to include drains or perforations to make sure you can remove the supports,” said Martinez.
In the end, the decision on whether or not to hollow out a design often depends on the scale of the design.
Explore Shapeways Resources on Full Color 3D Printing
Learn even more about the importance of full color in 3D printing today by watching a replay of the webinar, ‘File Preparation for Texture Based Full Color 3D Printing’ here. Co-presented by Shapeways and Mimaki, viewers can follow the second webinar focused on full color but more specifically, on advancing forward to 3D file preparation and more advanced options and techniques–as related to manufacturing for the Mimaki 3DUJ-553 and the compact Mimaki 3DUJ-2207.
An impressive amount of detail and color gradients can be achieved with High Definition Full Color, accentuated with the topics discussed in the webinar. Full-color 3D models are available in either a standard or matte finish. Final parts can be coated, and hardware-like screws can be easily attached for hanging requirements or other preferences.
About Shapeways
Enjoy the benefits of this advanced technology and a wide range of materials from Shapeways for 3D printing your creations with accuracy, complex detail, and no minimum or limits in terms of mass customization or single part orders. Shapeways has worked with over 1 million customers in 160 countries to 3D print over 21 million parts! Read about case studies, find out more about Shapeways additive manufacturing solutions, and get instant quotes here