
At Shapeways, each production job is unique, beginning its journey from the instant a 3D model is uploaded. At that point, proprietary software automatically prompts the manufacturing process into motion; however, businesses with larger-volume orders can benefit from working with the User Application (UA) Team directly.
This department controls production of quality parts, made to the customer’s specifications—whether they are intended for a component in an important aerospace application like a drone, a large-scale, 3D printed interior piece for an architectural firm, full-color miniatures for companies centered around the gaming industry, or perhaps even an electronic measuring device for home-brewing craft beer.
The UA Team also works with customers in a wide—and continually expanding—range of other applications. With the team motto of ‘bridging the gap,’ the UA Team specializes in the the technical side of communication:
“We are there to help with any and all questions about design, materials, or the processes that make our customers’ models come to life,” says Zach Dillon, User Application Team Lead at Shapeways.
Read on to learn how working with the UA Team could help take you from concept to manufacturing successfully.
Designing the 3D Model to Fit the Material and Technology
Whether businesses are engaged in 3D printing or relying on more traditional manufacturing techniques, manufacturing can be challenging in the beginning in terms of choosing the proper materials, technology, and parameters. The process of uploading a model to Shapeways is streamlined. In many cases customers need do nothing more than create an account, upload their 3D models, choose materials and finish, and receive quality, customized 3D prints in the mail; however, sometimes it just isn’t that easy. And that is where the Shapeways User Application Team comes in—managing design, materials, and manufacturing.
Each build is unique, presenting the potential for varying product requirements every time. Part geometries, materials, and ultimately, the strategy of the build all figure predominantly into the jobs of the UA Team daily. These are the people at Shapeways who chaperone each part from the beginning of its journey—to the finish line.

Analyzing and Fixing 3D Files to Ensure Printability
The first stop in the journey of a 3D model is design analysis. This is a critical phase, because if the file is not printable, extra measures need to be taken. 3D models may initially be deemed unprintable due to the following:
- Weak geometries
- Wall-thickness
- Orientation
- Intricate engraving details
- Texture
In some cases, designs may simply be unprintable because they are not within guidelines. For customers working with a set of product requirements, a one-on-one consultation with the UA Team could help them cross the final hurdle to start scaling their manufacturing.
The consultation usually includes a deeper analysis to explore the current 3D model, why it may or may not survive the manufacturing process, what types of post-processing will be necessary, and what to expect in the printed product. At that point, customers may decide to re-work their design, choose another 3D printing material for a better fit, or explore other technologies—all key factors in leading them to the next level in additive manufacturing.
“Our goal is to make the customer experience as seamless as possible,” says Matthew Nadler, User Application Materials Specialist at Shapeways. “We unlock all that Shapeways has to offer for our customers, and enable them to leverage our full capabilities.”
Consulting with the UA Team for Customized Build Trays
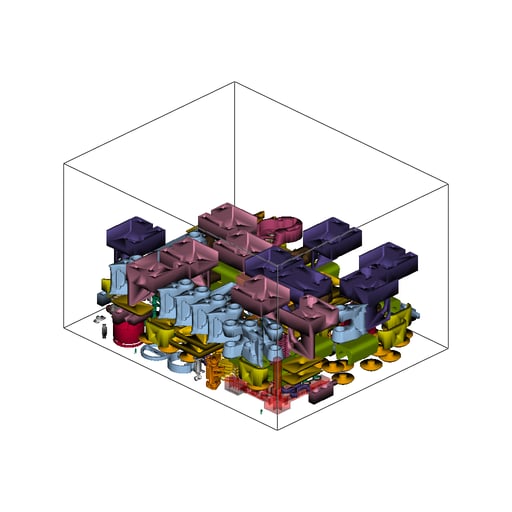
Shapeways relies on proprietary purpose-built software to ensure excellence in quality management, but also allows customers printing in Nylon 12 [Versatile Plastic] to take more control during the uploading and ordering process using a feature in 3D Tools, where there is an option to set the orientation and lock in the desired details for production. Once the model is deemed printable, customers that require bulk production of their parts may benefit from working with the UA team to custom design the build tray within the hardware.
The build tray can be packed with literally thousands of parts, all placed strategically for the best outcome in quality. Strategic orientation within the build process is known as nesting, sometimes involving complex strategy similar to a puzzle. Smart packing leads to quality products.
Scaling Up May Require More Than Additive Manufacturing
The User Application Team is well-versed in offering a wide range of recommendations. Depending on the customer’s product development stage, the UA Team is there to work with designers and businesses in offering customized solutions. These solutions may include additive as well as traditional manufacturing processes. The aerospace and medical industries, for example, often rely on both to reap the benefits these different manufacturing technologies have to offer.
The key to success for any business engaged in manufacturing is to remain open, adaptable, and realistic regarding the requirements and amount of production volume necessary for any build. This is precisely why Shapeways remains agnostic to any particular materials or technology. While the UA Team may recommend selective laser sintering for one project, injection molding could be a better choice for a business scaling their production en masse into the thousands or millions.
Issues may arise regarding printability, but a 3D model initially deemed problematic could still offer great promise after further analysis and a transition to different materials, methods, or manufacturing. The UA Team encourages taking a further look, providing a hands-on approach to manufacturing quality, high-performance parts with accuracy and repeatability.
About Shapeways
Contact Shapeways now to enjoy the benefits of advanced technology and materials for manufacturing your creations with accuracy, complex detail, and no minimum or limits in terms of mass customization or single part orders. Shapeways has worked with over 1 million customers in 160 countries to make over 20 million parts! Read about case studies, find out more about Shapeways solutions, and get instant quotes here.