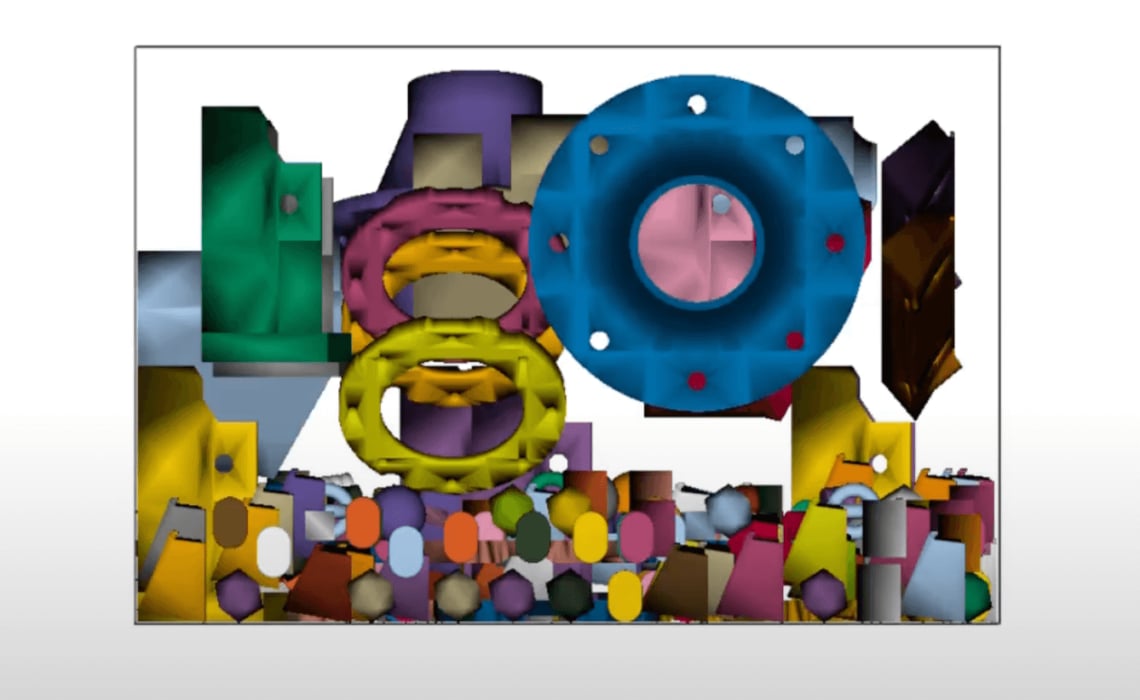
The story of every Shapeways product begins with the spark of an idea, a design, a model—and the industrial 3D print which is born as soon as it is analyzed for 3D printability, and assigned to a machine and a tray. From there, the 3D model is packed strategically with hundreds or even thousands of parts.
And if it’s really true that doing puzzles on a routine basis continues to raise intelligence levels, then the production engineers at Shapeways should continue to shine with profound brilliance. After all, packing parts for 3D printing or ‘nesting,’ is often compared to the 80’s game Tetris. The satisfaction and mental stimulation found in moving pieces around is similar as 3D print builds are packed for success with the assistance of colorful automated visualization. And while the addiction of the videogame is what keeps players coming back for more, the quality parts produced after ‘smart packing’ are what bring Shapeways customers back time and time again.
Games like Tetris and the 3D printing puzzle of nesting share a few things in common: goal-setting from the outset, strategy, and concentration. The stakes are much higher in industrial manufacturing though. For 3D printing engineers at Shapeways nesting 3D prints together, strategic packing is considered early in the process–and the number one goal is quality in parts. This holds true whether they are manufacturing a detailed 3D printed architectural model or a high-performance 3D printed automotive part. Each additive manufacturing build is different, meaning that each 3D printed puzzle in terms of nesting is unique too.
Leveraging 3D Printing Nesting Software for Smart Packing and Orientation
While nesting was previously a manual process, now Shapeways leverages proprietary purpose-built software, which includes 3D printing nesting software, ensuring quality, and consistent 3D printed parts. Streamlined, dense packing of parts reduces the height of the build platform, saves materials, and speeds up production.
Nesting software interlocks and rotates the 3D printed models, sorting them and condensing them as tightly as possible too. Balance is important, and different shapes and sizes of parts have to be taken into consideration—especially when they are fragile and may need to be placed at the top, rather than sitting under powder where there could be the potential for damage in a large build.
“The 3D printing nesting software does the hard thinking for us in terms of whether or not a part fits into the spaces available in a build tray,” said Zach Dillon, User Application Team Lead at Shapeways.
Proper orientation is one of the most principal elements in 3D printing and the nesting process. Typically defined as a way to align or position an item, in terms of 3D printing, orientation at Shapeways is related to how industrial parts are placed together in the build tray. This presents the opportunity to make sure a product reaches its true potential for success; in fact, nearly every ingredient for making a quality product comes together in the orientation.
Shapeways typically chooses the best orientation for nesting of 3D parts that customers upload, as models must be matched with compatible 3D printing materials and technology. In some cases, a communicative effort is required between Shapeways and the customer for the best outcome in 3D printing a complex part. Although online customization options are available for materials like Nylon 12 [Versatile Plastic], the User Application team at Shapeways can work with customers who have orientation requests or concerns about what type of materials to use—and questions about when to use 3D printing over conventional manufacturing.
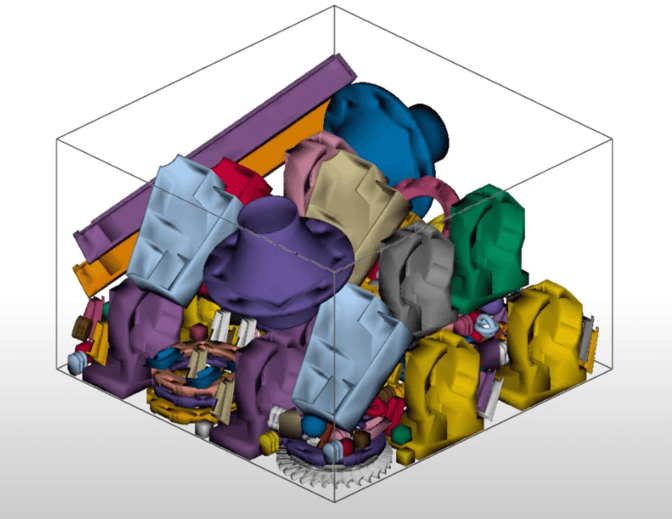
What 3D Printing Technologies Use Nesting?
Nesting is typically used in powder-based 3D printing technologies like Selective Laser Sintering (SLS) and Multi Jet Fusion (MJF).
Selective Laser Sintering
Yielding higher accuracy and repeatability than most techniques, Selective Laser Sintering (SLS) is a powder-based 3D printing process performed from the small to large scale, often requiring many parts to be nested in one build. SLS technology is one of the most popular and powerful industrial methods being used in additive manufacturing, with thin layers of powder dispersed over the build platform to begin the process. A CO2 laser then traces the pattern of the 3D design in the powder, continuing to fuse each consecutive layer together until the product is complete.
SLS industrial 3D printers can range in build volume size; for example, smaller printers may have a build volume of 200 mm x 250 mm x 330 mm, but printers from EOS can range in build volume from 650 mm x 350 mm x 550 mm to 700 mm x 380 mm x 580 mm, with a layer thickness of 100 to 120 microns.
Shapeways offers the following materials for SLS 3D printing:
Find out more about the material properties and design guidelines for each Selective Laser Sintering 3D printing material here.
Multi Jet Fusion
Multi Jet Fusion (MJF) is another powder bed fusion 3D printing process, developed by HP as a progression from their experience in inkjet technology. As powder is deposited across the build area, both fusing and detailing agents help build the 3D printed structure, with each layer fused together via infrared heat. Again, with the ability to avoid support structures and pack builds with many parts, much higher production runs are possible.
Shapeways offers the following materials for MJF 3D printing:
Find out more about the material properties and design guidelines for each Multi Jet Fusion 3D printing material here.
Working with the User Application Team to Optimize 3D Printing Production
The key to quality is ensuring each part is situated in the 3D print build tray so all parts are created with the utmost consistency and accuracy. Smart packing is key to optimization, allowing for parts to be placed correctly, and also keeping machines in good working order by running them consistently with maximum builds for efficiency.
When Shapeways customers print in large volumes, being able to work directly with the User Application team to optimize nearly every aspect of production is a huge benefit.
“We have to take everything into consideration from how larger 3D printed parts will affect others around them to how they will all be unpacked and cleaned in post-processing,” said Dillon.
“Building these trays and filling them with parts can be an art form,” said Dillon. “Each layer of 3D printed parts must be homogenous, especially in terms of temperature. There can be a fight against heat. You don’t want to be dealing with one layer in a build that is lower-sintered and another that is higher-sintered right next to one another.”
Smart Packing Leads to Additive Manufacturing Sustainability
With nesting of parts, customers experience one of the greatest benefits in 3D printing: speed in turnaround. By consolidating many parts in one build, Shapeways engineers complete multiple 3D printing projects simultaneously. It’s no secret that industrial 3D printing powder can be expensive. Both SLS and MJF technology allow for savings and easy recyclability in powder, build after build.
Unsintered powder bunches around parts as they are 3D printed, stabilizing structures, and eliminating the need for support structures. This leads to much greater design freedom as designers are able to engineer parts without having to compensate for intricate supports. No requirements for supports means less use of materials ultimately, reducing the potential for damage in post-processing, and forcing the need for repeated 3D printing.
In re-using powder while preserving material integrity, Shapeways contributes to increased sustainability in manufacturing, lessening environmental impact.
In working with the UA team, Shapeways customers optimize production and reach collaborative goals in use of 3D printing materials and technology:
- The Israeli bee pollination experts at BeeHero chose to manufacture with Shapeways using Nylon 12 and SLS technology for comparable quality over conventional technology, looking toward added texture, strength, and flexibility in parts. Because their end users are invested in expensive technology for pollination—and products like the BeeHero smart hives—quality in parts is critical.
- Shapeways worked with Dana-Farber Cancer Institute a decade after their initial installation to overhaul a complex zebrafish display involving a massive transfer of 3D files and manufacturing of parts via SLS 3D printing. 477 zebrafish models were 3D printed in Nylon 12 [Versatile Plastic] and mounted in the Dana-Farber lobby, embedded with high-tech innovation, illuminating when prompted, and displaying donor information.
- Dutch fashion designer Anouk Wipprecht has worked with Shapeways for many years to prototype and manufacture complex parts for pieces like the HeartBeatDress, featuring a series of parts 3D printed with Nylon 11 [PA11 (SLS)] and SLS 3D printing.
- For 67 Designs, SLS technology with Nylon 12 [Versatile Plastic] was the ticket to 3D printing customized high-end vehicle accessories. CEO Gavin Stener is dedicated to 3D printing and plans to continue using the technology in a production environment for as long as possible, even as demand for his sturdy mounting devices for off-roading vehicles continues to grow.
- Tilt Hydrometer was drawn to working with Shapeways because of the ability to prototype with ease using Nylon 12 [Versatile Plastic]. Their team designed over a hundred prototypes to perfect their 3D printed free-floating hydrometer, with thousands of beer lovers depending on the devices to measure sugar during fermentation.
“In manufacturing, we are bringing parts into the real world—out of a safe digital space where no physics like gravity have been applied yet,” said Dillon. “Ultimately it would be great if we could just say ‘one printer, one part,’ but that would be unrealistic. There has to be a balance between machine efficiency and quality.”
Many current customers have been working with Shapeways since the early days, and these businesses have grown together over time—along with access to advanced new materials, 3D printing technologies, and endless options for customization.
About Shapeways
Enjoy the benefits of this advanced technology and a wide range of materials from Shapeways for 3D printing your creations with accuracy, complex detail, and no minimum or limits in terms of mass customization or single part orders. Shapeways has worked with over 1 million customers in 160 countries to 3D print over 21 million parts! Read about case studies, find out more about Shapeways additive manufacturing solutions, and get instant quotes here.