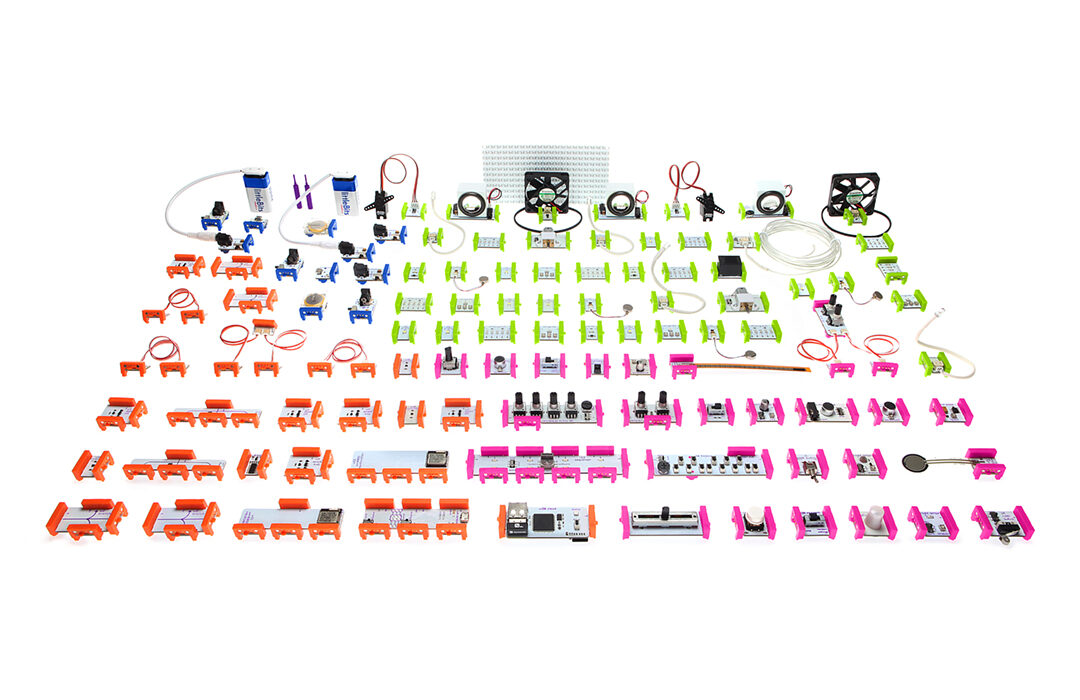
We wish the circumstances were different, but unfortunately the marketplace won’t be available in the way it existed before July 2024. We understand this has had a considerable impact on some of our marketplace shop owners and their customers, which we lament. Below we explain what led to this change, and provide links for additional information.
In July of 2024, after experiencing mounting financial difficulty, Shapeways Inc. filed for bankruptcy. In November of 2024 the management team of the Eindhoven factory along with two of the original Shapeways founders – both of whom have been out of the business for over a decade – joined together to resurrect the company. The new management team has completed the purchase of all available Shapeways IP assets. Unfortunately, all marketplace data was lost in the bankruptcy – we could not acquire it, nor was it available to be acquired. Additionally, the technology that the marketplace ran on was outdated and not scalable. Due to this combination of factors beyond our control, the marketplace cannot be revived as it previously existed. We still believe in the Shapeways Shops concept and are actively pursuing new ways to replace this service for the Shapeways community. This exploration will take time and we humbly ask for your patience on this journey.
We are building a small group of former shopowners to be advisors and a sounding board during this exploration. If you would like to be an active contributor on our journey to define the best solution, please contact us at [email protected].
To learn more about the recent changes at Shapeways and what to expect in this new chapter, see our most recent Press Release. To get to know our new CEO, Marleen Vogelaar, and her vision for Shapeways moving forward, see her letter to our customers and community. If you have specific questions about the marketplace including account data and the status of orders placed before the bankruptcy, refer to our FAQ. For any questions that are not answered in the above documents, please contact us.
Finally, to receive Shapeways announcements via email, please join our mailing list.