Industrial manufacturing encompasses a vast world of production, driven by innovation and consumer demand, materials, and machinery. In the past decade especially, additive manufacturing (AM) has taken its rightful place in the world of technology, increasingly relied upon by businesses and individuals at every level—set apart as an additive method creating structures layer by layer, allowing for reduced waste in materials. Meanwhile, traditional manufacturing is known for subtractive methods that carve out industrial parts using sheer force, relying on processes perfected throughout many decades with computerized direction and automated precision.
Additive Manufacturing Offers More Choices and More Freedom in Design
Relying on popular methods like Selective Laser Sintering (SLS), for example, to heat up powder particles and meld them together into a prototype or part, or Binder Jetting for fusing together stainless steel particles via a binding agent, additive manufacturing offers many new and exciting options in manufacturing. With the ability to create complex geometries previously impossible through traditional methods, unprecedented freedom is available in design and production, from the small to the large scale. In comparison to traditional manufacturing, there are minimal restrictions with a multitude of options for materials as well as a wide range of choices in terms of affordability, whether choosing thermoplastics or metal.
Maximizing customization while also minimizing the need for inventory is another benefit many businesses never considered possible, along with the possibility of cutting out warehouse space altogether. With on-demand 3D printing, custom parts can be produced based on need, in small volumes with the same accuracy and repeatability.

Traditional Manufacturing Empowers Repeatability and Mass Production
Conventional methods continue to stand the test of time, offering undeniable power in production. With the ability to manufacture thousands—and even millions—of parts in mass production without any deviation in quality or detail, traditional manufacturing is often the most proficient route for satisfying customer demand.
Similar materials may be available also for customers who were previously engaged in additive manufacturing but have grown to the point where moving up to a different process is more suitable. This is evidenced in methods like CNC machining and injection molding especially.
Computer Numerical Vontrol (CNC) Machining
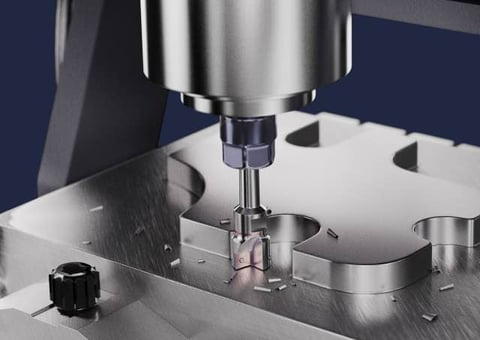
Pre-programmed computer software controls the subtractive manufacturing of industrial parts, issuing instructions centered around a 3D file. Performed through a variety of methods such as milling, drilling, turning, and cutting, CNC machining offers outstanding dimensional accuracy in parts, capable of surpassing 3D printing or other manufacturing processes—often making it a better fit for customers seeking more fine-tuned precision.
Shapeways offers a range of materials for use with CNC machining, some of which are used in additive manufacturing too, like thermoplastics, nylons, and metals.
Injection Molding

Patented in the 1870s, injection molding is commonly used for mass production of parts, relying on the use of molds which are typically made with plastic or steel.
Often heavily customized, depending on the requirements for specific applications, the molds can be used with materials like thermoplastics, nylons, or metal. The materials are heated to a molten state and then left to cool inside the molds, solidifying into the desired industrial part. There is generally little need for post-processing, with the molds being used over and over, offering incredible repeatability in parts for productions on the large scale.
The Journey: Transitioning from Additive to Traditional Manufacturing
For most businesses, the manufacturing goal is to make quality parts that last. Weighing out the pros and cons and making a final decision can be overwhelming at first, not to mention dealing with budget concerns over investments in hardware, software, and materials. Shapeways is a world leader in digital fabrication, but also remains agnostic in terms of all technology.
“Our focus is on working around customers’ needs in terms of matching the correct materials and processes to a specific application,” says Zach Dillon, User Application Team Lead.
Key points in choosing additive manufacturing usually boil down to the infinite level of innovation possible in 3D design, along with the ability to customize products intensively. Many Shapeways customers are dedicated to AM processes, and tend to use them as long as possible, especially because they are able to 3D print hundreds or even thousands of parts in one run. If customer demand has increased exponentially though, it could make greater economic sense—as well as increasing speed and efficiency—to scale up to mass production, using traditional methods for large volumes of identical parts.
Today, many businesses also rely on different types of hybrid technology. This could mean that they rely on a mixture of AM processes and CNC machining, for example, at one facility, or they may have turned to machinery that encompasses both AM and traditional manufacturing all in one. For businesses requiring true versatility, hybrid technology can be the answer in terms of having it all in terms of retaining all the benefits possible, with AM complementing traditional manufacturing, and vice versa.
Learn More about Working with Shapeways
Contact us now to find out more about which technology suits your needs, enjoying the benefits of 3D printing and traditional manufacturing without having to spend precious business capital on advanced hardware, software, or material inventory.
Find out more about manufacturing your creations with accuracy, complex detail, and no minimum or limits in terms of mass customization or single part orders. Shapeways has worked with over 1 million customers in 160 countries to make over 20 million parts! Read about case studies, find out more about Shapeways solutions, and get instant quotes here.